Při výběru frézovacích nástrojů je třeba vzít v úvahu možnosti obráběcích strojů, zamýšlené metody frézování, programování, upínací přípravky a držáky.
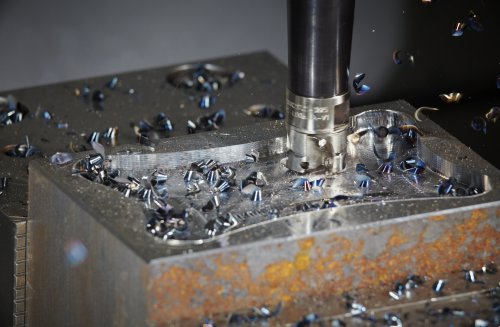
Techniky frézování a technologie obrábění se neustále vyvíjejí, a proto stále více výrobců forem využívá tohoto rozvoje pro optimalizaci obráběcích procesů, snižování počtu cyklů a dosažení mnohem lepší kvality povrchu tvarových částí forem. Faktory, jako jsou možnosti obráběcího stroje, metody frézování, programování, upínací přípravky a držáky, jsou při výběru obráběcího nástroje nezbytnou součástí tohoto procesu. Neméně důležitá je schopnost analyzovat opotřebení břitových destiček s cílem maximalizovat životnost nástroje a předpovědět jeho využití v aplikacích výroby forem. Dnešní rychlé a výkonné obráběcí stroje s pokročilými funkcemi programování jsou nezbytné při využívání nejmodernějších obráběcích nástrojů a zavádění vysoce účinných technik obrábění. Vysokorychlostní frézování a frézování vysokým posuvem jsou dvě oblíbené metody vyžadující pro úspěšnou operaci určitý typ fréz. Techniky frézování Vysokorychlostní (neboli dynamické) techniky frézování jsou stále populárnější. Jsou zvláště účinné při použití monolitních karbidových obráběcích nástrojů. Tato metoda frézování je optimalizovaným hrubováním, v němž se kombinuje velká hloubka řezu s relativně malým radiálním záběrem při obrábění oceli. Tato technika je také účinná při obrábění materiálů o tvrdosti 60 HRC a větší. Při frézování vysokým posuvem se doporučují velké vyměnitelné břitové destičky, které umožňují odfrézovat většinu materiálu. V zásadě tento proces začíná s relativně velkými vyměnitelnými břitovými destičkami pro hrubování a pokračuje přes vyměnitelné kulové frézy s menším průměrem až po monolitní karbidové frézy, které se používají ve finální fázi obrábění formy. Vhodné průměry fréz se určují na základě vlastností formy – například dle rohových rádiusů. Vyměnitelné břitové destičky pro frézování vysokým posuvem jsou obvykle průměru 15 mm (0,62 palce) a větší. Pokud je třeba použít menší frézy, doporučujeme monolitní karbidové stopkové frézy. Břitové destičky pro frézování vysokým posuvem se mohou lišit v závislosti na materiálu obrobku, nicméně ve většině případů je třeba použít povlakované PVD nebo CBN břitové destičky. Pokud jde o geometrii břitové destičky, trojúhelníkové poskytují nejnižší možný úhel nastavení oproti kruhovým nebo čtvercovým destičkám. Malé úhly nastavení zajišťují mnohem tenčí třísku, která zase vyžaduje vyšší posuvy, aby se uchovala správná tloušťka třísky pro geometrii destičky. Menší úhel nastavení také směřuje řezné síly axiálním směrem, tlačí nahoru do vřetene, které je tak stabilnější a snadněji ovladatelné. Vyšší úhly nastavení vedou k tlustějším třískám, což vyžaduje menší úpravy v rychlosti posuvu. Vedou také k větší radiální síle, což způsobuje vibrace a namáhání ložisek vřetene. Pro vysokorychlostní frézování se obvykle používají monolitní karbidové čtyřbřité rohové frézy s dlouhými břity a profilem pro dělení třísek - ty rozdělují třísky na malé a snadno zpracovatelné, což vede k lepšímu úběru materiálu a odstranění třísek z oblasti řezu i stroje. Kromě toho plná délka řezu a profily pro dělení třísek společně s vysokorychlostním frézováním vedou k větší produktivitě a výrazně delší životnosti nástrojů díky rovnoměrnému zatížení. Při frézování vysokým posuvem by fréza měla být v záběru celým průměrem, co se ale týče šířky destičky, neměla by zabírat méně než její polovina. Záběr v celém průměru je možný díky tomu, že vysokorychlostní frézy účinně směřují řezné síly do vřetene frézy v axiálním směru a jsou tak vyvážené. Frézy se záběrem menším, než je polovina šířky destičky, budou více vibrovat, protože řez je nevyvážený. U vysokorychlostního frézování se používají stejné obráběcí nástroje jako u frézování vysokým posuvem (vyměnitelné břitové destičky a monolitní karbidové stopkové frézy). Nicméně při tomto způsobu obrábění se musí využívat geometrie, které umožňují vysoké otáčky a rychlosti posuvu, ale zmírňují zatížení v protikladu k velké zátěži. I když jsou frézy pro vysoký posuv s dlouhým vyložením účinné, nemohou při použití ve vysokých rychlostech pracovat s takovou rychlostí jako nástroje s kratším vyložením, pokud se ovšem nepoužijí specializované držáky nástrojů pro snížení vibrací nebo pokud se výrazně nesníží řezná rychlost. Když nástroj s dlouhým vyložením pracuje při vyšších rychlostech, než je doporučeno, zvýší se vibrace, což zase vede k vyštipování břitu a jeho předčasnému opotřebení nástroje. Vyhodnocení opotřebení břitových destiček Maximální životnost nástroje a předvídatelné používání nástroje pro zachování přesnosti obrábění a snížení opotřebení obráběcích nástrojů jsou klíčové faktory pro optimalizaci pracovních postupů při obrábění forem. Nástrojárny musí znát různé typy poškození břitových destiček a opotřebené destičky prozkoumat s cílem určit příčinu vady. Při zkoumání destičky je třeba použít stereoskop s dobrou optikou, odpovídajícím osvětlením a zvětšením minimálně 20x, což přinese velký užitek při určování příčin vedoucích k předčasnému opotřebení břitové destičky. Existuje osm běžných poškození břitové destičky. Z nich je třeba při frézování forem vysokým posuvem sledovat opotřebení hřbetu nástroje, teplotní praskliny a vyštipování břitu. Nicméně používání nevhodných destiček může vést k výskytu dalších pěti typů poškození. 1. Opotřebení na hřbetu nástroje je rovnoměrné a dochází k němu postupem času tím, jak se materiál opotřebovává nebo jak se otupuje řezná hrana destičky. Při určování běžného opotřebení hřbetu nástroje se podél řezné hrany nástroje vytvoří relativně jednotné opotřebení. Čas od času se opracovávaný materiál dostane přes řeznou hranu a zvětší zřetelné opotřebení na destičce. Pro eliminaci běžného opotřebení hřbetu nástroje je důležité využít nejtvrdší třídu břitové destičky, která se nebude vyštipovat, a použít také nejvolnější řeznou hranu, aby se co nejvíce snížily řezné síly a tření. Na druhou stranu, rychlé opotřebení hřbetu často vzniká při obrábění abrazivních materiálů, jako například tvárné litiny, slitin křemíku a hliníku, slitin vznikajících při vysokých teplotách, cementačních nerezových ocelí, slitin berylia a mědi a slitin karbidu wolframu. Rychlé opotřebení hřbetu nástroje se projevuje stejně jako běžný otěr na hřbetu. Eliminovat vznik tohoto rychlého otěru na hřbetu lze použitím tvrdších břitových destiček nebo destiček povlakovaných karbidem, které jsou odolnější vůči opotřebení. 2. Vymílání na čele je kombinací difuze a abrazivního opotřebení způsobující v destičkách trhliny. Teplo generované třískami způsobuje, že částečky cementovaného karbidu se rozpouštějí a rozptylují se v řezu, čímž se na horní straně destičky vytváří výmol. Ten se zvětšuje, až nakonec způsobí odlomení hřbetu destičky, deformaci nebo může vést k rychlému opotřebení hřbetu. I když ochranu před vymíláním na čele zajistí jakékoli běžné povlakování, doporučuje se povlakování oxidem hliníku. 3. Když se fragmenty obrobku tlakem zapečou do řezné hrany břitové destičky, což je dáno chemickou přilnavostí, vysokým tlakem a dostatečně vysokou teplotou v zóně řezu, vytvoří se na břitu nárůstky. Ty se mohou odlomit a někdy se spolu s nimi odlomí i část destičky, což vede k rychlému opotřebení - vyštipování břitu či vzniku otěru na hřbetu. Nárůstky lze rozeznat pomocí nepravidelných změn ve velikosti obrobku nebo jeho povrchu nebo podle toho, že se na horní části nebo hřbetu břitové destičky objeví lesklý materiál. Nárůstky se dají regulovat zvýšením rychlosti frézování a posuvu, použitím destiček povlakovaných TiN a výběrem břitových destiček s takovou geometrií, která snižuje síly, a destiček s hladšími povrchy. 4. Vyštipování břitu je způsobeno mechanickou nestabilitou, která je často způsobena málo tuhým nastavením, špatnými ložisky nebo opotřebovanými vřeteny, tvrdými vměstky v obráběném materiálu nebo přerušovaným řezem. Vydrolování ostří lze předejít správným nastavením stroje, minimalizací výkyvů, používáním honovaných břitových destiček, regulací nárůstků a využitím tvrdší třídy břitových destiček a/nebo silnější geometrie řezné hrany. 5. Termální mechanické poškození břitu je způsobeno kombinací náhlých výkyvů teploty a mechanických otřesů. Trhliny způsobené otřesy se tvoří podél hrany břitové destičky a mohou způsobit vydrolování ostří. Známkou teplotního mechanického poškození jsou četné trhliny kolmé na řeznou hranu. Je důležité odhalit tuto vadu ještě dříve, než dojde k vyštipování břitu. Teplotnímu mechanickému poškození lze předejít správným používáním chladicí kapaliny nebo ještě lépe jeho úplným odstraněním z procesu, a to použitím odolnější třídy břitové destičky a využitím takové geometrie, která snižuje tvorbu tepla. 6. V důsledku nadměrného zahřívání spolu s mechanickým namáháním se tvoří deformační hrana, což je často případ obrábění forem. Při vysokých rychlostech a posuvu nebo při obrábění tvrdých ocelí, kalených povrchů a vysokoteplotních slitin se vytváří značné teplo. V důsledku toho karbidové pojivo nebo kobalt v břitové destičce změkne. Deformace hrany se dá regulovat použitím odolnější třídy břitové destičky s menším obsahem pojiva, snížením řezné rychlosti a posuvu a využitím geometrie, která snižuje vyvíjenou sílu. 7. Vruby na ostří se stanou výraznějšími tehdy, když se vruby a trhliny objeví na břitové destičce v hloubce záběru. Předcházet takovému opotřebení lze změnou hloubky záběru při použití více průchodů; použitím nástroje s větším úhlem nastavení; při obrábění vysokoteplotních slitin zvýšením řezné rychlosti; snížením rychlosti posuvu; pečlivým zvětšením honování v oblasti hloubky záběru a předcházením nárůstků, zvláště u nerezových ocelí a vysokoteplotních slitin. 8. Mechanické zlomy na břitové destičce se vyskytují tehdy, když je aplikovaná síla větší než vlastní pevnost řezné hrany břitu. Ke zlomení může přispět i jakékoli z výše uvedených opotřebení. Mechanickým zlomům lze předcházet eliminací všech typů opotřebení, vyjma běžného opotřebení hřbetu nástroje. K účinným preventivním metodám patří využití třídy odolnější vůči otřesům, výběr silnější geometrie břitové destičky, použití tlustší destičky, snížení rychlosti posuvu a/nebo hloubky řezu, kontrola tuhosti nastavení a kontrola materiálu obrobku, zda neobsahuje tvrdé vměstky či zda nájezd do kusu bude hladký. Třídy fréz, geometrie, materiály a velikosti Většina výrobců obráběcích nástrojů vyvíjí nástroje s třídou a geometrií určenou pro specifické materiály. Při obrábění forem patří k těmto materiálům oceli P20, CPMV 10 a práškové kovy. Vybrat pro daný obráběný materiál správnou třídu a geometrii je velmi důležité, aby se předešlo předčasnému opotřebení nástrojů. Správný nástroj pro daný materiál navíc pomáhá zvýšit účinnost a předvídatelnost, což vede k menšímu počtu výměn nástrojů, nižší zmetkovitosti a menší nutnosti přepracování. Pokud je obráběn materiál o tvrdosti 52 HRC nebo měkčí, dají se s úspěchem použít nástroje z monolitního karbidu určené pro běžné obrábění. U tvrdších materiálů by se měly použít čelní stopkové frézy z monolitního karbidu s odlišnou geometrií a povlakováním, jako je například nitrát hliníku a titanu určený pro extrémně tvrdé materiály. Navíc pro monolitní karbidové nástroje existují speciální směsi povlaků, přičemž každý výrobce forem používá speciální povlaky. U fréz s vyměnitelnými břitovými destičkami se pro většinu extrémně tvrdých práškových kovů osvědčila geometrie a povlaky pro velmi tvrdé povrchy. Různé třídy břitových destiček a řezné drážky, které jsou na současných frézách k dispozici, umožňují optimalizovat obrábění tvrdších materiálů tvarových částí formy. Po určení typu frézy se musí vybrat také správný rádius obrábění. Rádius obrábění musí být menší než vnitřní rohový rádius formy. Pokud rádius nástroje odpovídá rohovému rádiusu formy, dojde k situaci známé jako tvrdý stop; na rozdíl od situace, kdy břit hladce oblouk vykrajuje. Pro dokončovací operace se doporučuje použít monolitní karbidové frézy s menším rádiusem. V současnosti jsou také k dispozici i karbidové frézy pro frézování vysokým posuvem. Stejný princip využívání rádiusů platí i pro hrubování – použití frézy s menším rádiusem, než jaký je na obrobku. A i když se při tomto postupu zanechává v rozích více materiálu, pomáhá to udržovat konzistentní, rovnoměrnou zátěž frézy i při všech následných dokončovacích operacích. Stejně podstatný význam, jaký má rádius frézy, má i její tuhost, přičemž klíčovou roli v tomto směru hrají úkosy / upínací kuželkužel frézy. Většina fréz má podbroušený nebo kuželový čep. Nástroje s podbroušeným čepem poskytují menší průměr, než je velikost břitu nad břity a pod průměrem stopky frézy. U nástrojů se zkoseným čepem je nejprve průměr řezu, poté oblast podbroušení, která je menší než tento průměr, a poté kužel až po průměr stopky. Většina fréz s dlouhým vyložením je zkonstruována s kuželovým čepem. Menší úhel úkosu znamená větší tuhost nástroje. Nicméně úkos je důležitý, protože eliminuje odírání stěn dutin formy. Při výběru co nejtužší frézy se musí vzít v úvahu úhel úkosu v dutině formy. Úkosy frézy by nikdy neměly být stejné nebo větší než je úkos formy. Například pokud má dutina formy třístupňový úkos na všech svých stěnách, mohou se použít nástroje s úkosem do 2,5 stupně. Chlazení Pokud se při obrábění forem uvažuje o používání chladicí kapaliny, většina vyspělých konstrukcí fréz a geometrií má optimální účinnost, když obrábění probíhá bez chlazení. Výjimku tvoří obrábění s olejovou mlhou, ale ta se musí používat po celou dobu. U těžce obrobitelných materiálů platí pravidlo, že chladicí kapalina se nepoužívá za žádných okolností, pokud ovšem není k dispozici olejová mlha. Držáky Pokud jde o držáky nástrojů, většina společností vyrábějících nástroje pro obrábění forem doporučuje držáky tlumící vibrace kombinované s použitím vyspělých fréz. Ani ten nejlepší nástroj v držáku běžného typu nedosáhne optimálního výkonu a životnosti, zatímco moderní držáky mohou životnost nástroje až zdvojnásobit. Klíčové je omezení vibrací, a to zvláště u nástrojů s velkou délkou vyložení a u frézování vysokým posuvem, a také při hrubování. Podstatné je, že konstrukce držáků tlumí vibrace a harmonické kmity generované při obrábění. Dráhy frézy a programování Díky správnému naprogramování dráhy frézy se zamezí nerealistickým požadavkům na frézovací nástroje při obrábění. Například při obrábění formy, kdy nástroj začíná obrábět roh, je třeba naprogramovat hladký přechod změny směru, aby se nevytvořil velký úhel záběru. To by mohlo nástroj neúměrně zatížit. Dobrým zvykem je naprogramovat oblouk, který je větší než rádius frézovacího nástroje. Takže pokud se použije fréza s rádiusem 50 mm (2 palce), v programu by se neměl používat rádius 25 mm (1 palec), ale raději větší vyrovnávací rádius. Naprogramování správných oblouků může být náročné, ale pokud se neudělá správně, může to vést k nežádoucím dráhám nástroje. V současné době existuje několik softwarových balíčků, které mohou uživatelům pomoci s programováním správné dráhy nástroje. Je také dobré využít služeb zkušeného programátora, který ví, jak využít zásady kontaktního oblouku. Cílem je vyhnout se zastavení stroje a určit správnou dráhu nástroje. Jakékoli zaváhání při vedení nástroje během změn směru vede ke generaci tepla, které se přenáší na nástroj. Teplo může zničit řeznou hranu frézy a její povlak a je třeba ho z řezné zóny odvádět včetně třísek. Shrnutí Díky lepšímu pochopení dnešních metod frézování a nástrojových technologií, stejně jako různých typů opotřebení a schopnosti tato opotřebení analyzovat, mohou výrobci forem svůj výrobní proces zefektivnit, snížit počet cyklů, zvýšit životnost a její stálost, zlepšit tolerance obrobků a jejich vzhled, dosáhnout vysoké kvality povrchu tvarových částí formy a menšího opotřebení v nástrojovém vybavení. Zpracovali Gary Meyers, produktový manažer, Copy Milling and Solid Carbide ze společnosti Seco Tools a Don Graham, manažer vzdělávání a technických služeb ze společnosti Seco Tools.
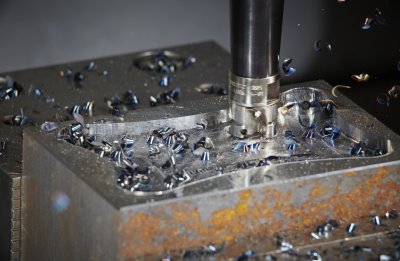 Při frézování vysokým posuvem je třeba předcházet zastavení a opětovnému zahájení obrábění v dráze nástroje, protože jakékoli zaváhání při vedení nástroje během změny směru vede ke generaci tepla, které se přenáší na nástroj. 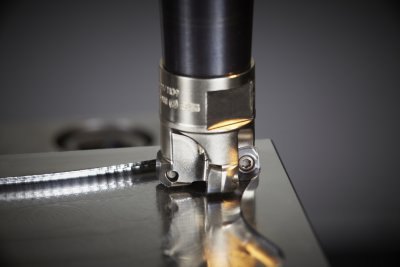 Během frézování vysokým posuvem by měly být frézy vedeny po celém průměru záběru a minimálně polovinou šířky destičky. Záběr v celém průměru je možný díky tomu, že frézy pro vysoký posuv účinně směřují řezné síly do vřetene frézy v axiálním směru a vytvářejí tak rovnováhu. 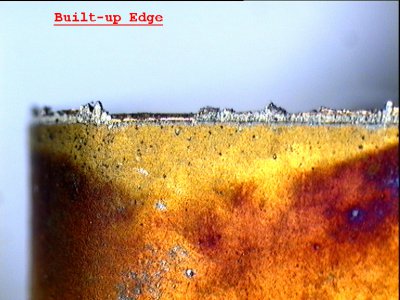 Řezná hrana s nárůstky 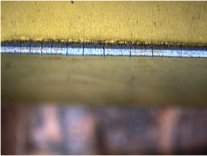 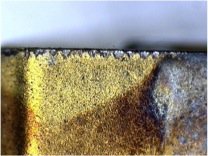 Tři nejčastější opotřebení při frézování vysokým posuvem jsou opotřebení hřbetu nástroje, teplotní praskliny a vyštipování břitu.
Společnost Seco Tools je předním světovým výrobcem vysoce výkonných obráběcích nástrojů. Produkce společnosti Seco zahrnuje kompletní program nástrojů a břitových destiček pro soustružení, frézování, vrtání, vystružování a vyvrtávání, doplněné i upínacími systémy nástrojů. S více než 25 000 standardních produktů tak společnost Seco kompletně pokrývá oblast obrábění kovů a vybavení obráběcích strojů od vřetena až po břity nástrojů. Společnost sídlí ve Švédsku, v městě Fagersta, a má zastoupení ve více než 50 zemích světa, spolu se 40 přidruženými společnostmi, distributory a prodejci. Více informací na www.secotools.com.
Seco Tools CZ, s.r.o. Londýnské nám. 2 639 00 Brno TEJKALOVÁ Alena Phone : +420-530-500-827 alena.tejkalova@secotools.com
|